At this point, it’s pretty evident what happened with AS1282 – a manufacturing issues, not an engineering one. However, the official NTSB report will take a year or two to come out, so if you don’t want to wait, a whistleblowers points to the cause of AS1282.
Before we get into the topic of today’s post, let me just say that the way mainstream media (and even some bloggers/vloggers) are covering the incident and other is, well, frustrating. Earlier this week, I watched a YouTube video accusing Alaska Air of ignoring potential warning signs when the NTSB already cleared the airline and said the warning light had nothing to do with the door plug incident. An AP article also suggested that two Boeing planes colliding on the ground as an issues with Boeing. And CNN equated UA328 with Boeing’s issues, even though that issue was with the engine manufactured by Pratt & Whitney.
I liken all of these issues as 1) sensationalization to get more clicks/views, 2) incomplete research, 3) inadequate understanding of the aviation industry as a whole, or 4) all of the above. I’m not saying I’m an expert, but beware of what you read/view out there, folks. I at least try to do my homework. Oh, and that video I mentioned earlier also placed the blame for the entire MAX debacle on Boeing. Yes, the company does carry a lot of fault for all of the aircraft’s issues, but you know who pushed for the 737 MAX with MCAS? The AIRLINES.
Whistleblower Points to the Cause of AS1282
In recent days, I’ve seen quite a few comments, interviews, etc., with former Boeing and claimed (but anonymous, obviously) current employees about the state of Boeing’s production process. However, this comment, which was reported on by Gary Leff, was quite revealing. And, if true, points to large, systemic issues at both Boeing and the subcontractor that actually makes 75% of every Boeing 737 – Spirit AeroSystems.
I’m not going to report the whole comment here – you can read it for yourself over on Leeham News – but I will highlight portions I find particularly interesting.
The mid-exit doors on a 737-9 of both the regular and plug variety come from Spirit already installed in what is supposed to be the final configuration and in the Renton factory, there is a job for the doors team to verify this “final” install and rigging meets drawing requirements. In a healthy production system, this would be a “belt and suspenders” sort of check, but the 737 production system is quite far from healthy, its a rambling, shambling, disaster waiting to happen.
As a result, this check job that should find minimal defects has in the past 365 calendar days recorded 392 nonconforming findings on 737 mid fuselage door installations (so both actual doors for the high density configs, and plugs like the one that blew out).
Ok, so most of the news I’ve been seeing says that Boeing removes the door plug to install the interiors, which I found an odd claim. Apparently, this isn’t the case, as the employee states the door/door plug supposed to arrive in its final state, and Boeing is supposed to verify their work. But before you go pointing fingers squarely at Boeing for not doing their job, it gets a bit crazier, never mind the fact that they’ve been finding more than one door-related issue per day in recent times. Yikes!
Now, on the incident aircraft this check job was completed on 31 August 2023, and did turn up discrepancies, but on the RH side door, not the LH that actually failed. I could blame the team for missing certain details, but given the enormous volume of defects they were already finding and fixing, it was inevitable something would slip through- and on the incident aircraft something did. I know what you are thinking at this point, but grab some popcorn because there is a plot twist coming up.
*grabs Hurricane popcorn*
The next day on 1 September 2023 a different team (remember 737s flow through the factory quite quickly, 24 hours completely changes who is working on the plane) wrote up a finding for damaged and improperly installed rivets on the LH mid-exit door of the incident aircraft.
See, Boeing employees did find improperly installed rivets on the subject door for AS1282. Now according to the employee, the team records their findings in the official system of record called CMES and their Slack-like system to start the corrective response called SAT. What happens next is interesting and a bit crazy.
Because there are so many problems with the Spirit build in the 737, Spirit has teams on site in Renton performing warranty work for all of their shoddy quality, and this SAT promptly gets shunted into their queue as a warranty item. Lots of bickering ensues in the SAT messages, and it takes a bit for Spirit to get to the work package. Once they have finished, they send it back to a Boeing QA for final acceptance, but then Malicious Stupid Happens!
The Boeing QA writes another record in CMES (again, the correct venue) stating (with pictures) that Spirit has not actually reworked the discrepant rivets, they *just painted over the defects*. In Boeing production speak, this is a “process failure”. For an A&P mechanic at an airline, this would be called “federal crime”.
Presented with evidence of their malfeasance, Spirit reopens the package and admits that not only did they not rework the rivets properly, there is a damaged pressure seal they need to replace (who damaged it, and when it was damaged is not clear to me). The big deal with this seal, at least according to frantic SAT postings, is the part is not on hand, and will need to be ordered, which is going to impact schedule, and (reading between the lines here) Management is Not Happy.
However, more critical for purposes of the accident investigation, the pressure seal is unsurprisingly sandwiched between the plug and the fuselage, and you cannot replace it without opening the door plug to gain access. All of this conversation is documented in increasingly aggressive posts in the SAT, but finally we get to the damning entry which reads something along the lines of “coordinating with the doors team to determine if the door will have to be removed entirely, or just opened. If it is removed then a Removal will have to be written.”
Note: a Removal is a type of record in CMES that requires formal sign off from QA that the airplane been restored to drawing requirements.
If you have been paying attention to this situation closely, you may be able to spot the critical error: regardless of whether the door is simply opened or removed entirely, the 4 retaining bolts that keep it from sliding off of the door stops have to be pulled out. A removal should be written in either case for QA to verify install, but as it turns out, someone (exactly who will be a fun question for investigators) decides that the door only needs to be opened, and no formal Removal is generated in CMES (the reason for which is unclear, and a major process failure).
Therefore, in the official build records of the airplane, a pressure seal that cannot be accessed without opening the door (and thereby removing retaining bolts) is documented as being replaced, but the door is never officially opened and thus no QA inspection is required.
This entire sequence is documented in the SAT, and the nonconformance records in CMES address the damaged rivets and pressure seal, but at no point is the verification job reopened, or is any record of removed retention bolts created, despite it this being a physical impossibility. Finally with Spirit completing their work to Boeing QAs satisfaction, the two rivet-related records in CMES are stamped complete, and the SAT closed on 19 September 2023. No record or comment regarding the retention bolts is made.
Goodness. What a mess! Boeing and Spirit employees are working in Renton, and though Spirit’s work has been crap, they try to get away with not making repairs and don’t do a good job with rework that they do. And its so confusing that we don’t really know who’s at fault for not recording the removal of the bolts! Ultimately, this is what we’re going to have to wait for the NTSB report to find out.
As for where are the bolts? According to the employee, the NTSB isn’t going to find them. Anywhere.
So, where are the bolts? Probably sitting forgotten and unlabeled (because there is no formal record number to label them with) on a work-in-progress bench, unless someone already tossed them in the scrap bin to tidy up.
FAA Recommend 737-900 Plug Door Inspections
It’s worth noting that the FAA is now recommending that airlines inspect the door plugs on Boeing 737-900ER, which is virtually identical to the one found on the Boeing 737 MAX 9. The FAA notes that this recommendation comes as undisclosed airlines have found loose bolts on 737-900ERs, but wouldn’t elaborate. However, this isn’t a mandatory inspection – just an advisory. And, honestly, the risk is minimal. The Boeing 737-900ER has been flying for a long time now. For example, the oldest 737-900ER in Alaska’s passenger fleet – N305AS – is approaching 23 years old.
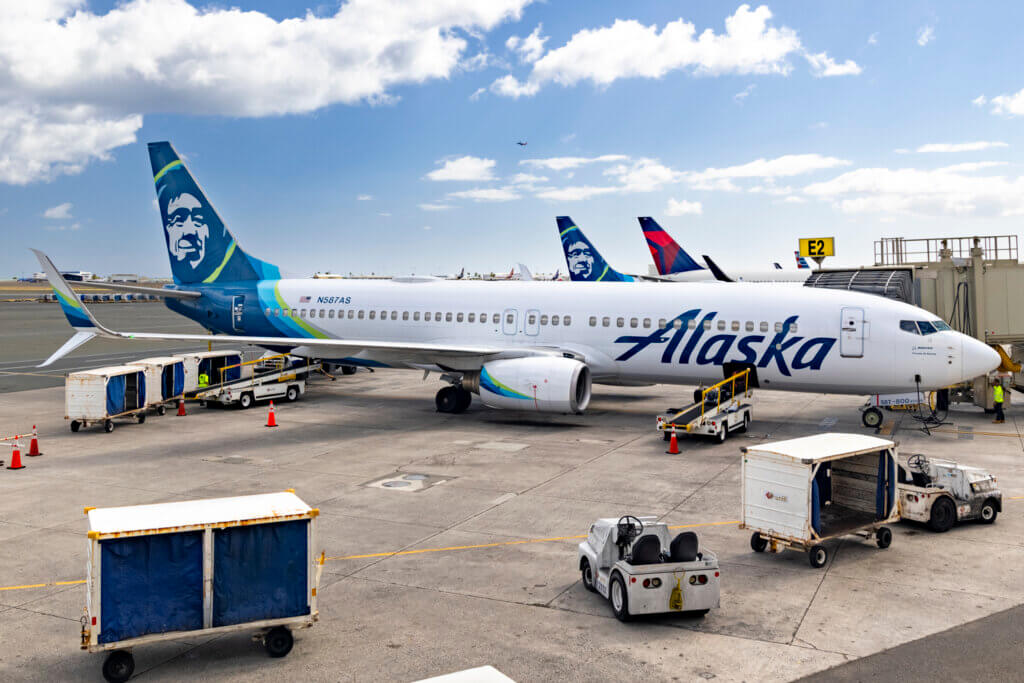
Whistleblower Points to the Cause of AS1282, Final Thoughts
Woo. That’s a lot of info. But it really reinforces the theory that this is a process issue, not an engineering one. Thank goodness that a whistleblower points to the cause of AS1282, as it really is informative. That said, we do still need the investigation to pinpoint where things really broke down, though I suspect that the blame will ultimately lie with Boeing.
Now, I’m not a Boeing apologist, but I think it’s outlandish that people are saying they won’t fly any Boeing aircraft at all now. Boeing is a great company filled with outstanding people that’s lost its way in the pursuit of profits, though that’s, ultimately, harming their profits. This is an important lesson McDonnell Douglas executives, which are who took over management in post-merger Boeing (wanna guess why?), should have learned from their DC-10 debacle. But here we are.
Hopefully, all of this – and all the other crap that has happened with the MAX and 787 – will be a wakeup call to Boeing’s bored to put quality first. However, I’m not holding my breath. Of course, I won’t actively avoid Boeing aircraft, either. I have no issue flying on a Boeing 737 MAX 8, or any of their other products at this point in time, and do fully expect this issue to be fully rectified at some point in time.